In the dynamic landscape of the food packaging industry, the choice of a burger box making machine is pivotal for businesses aiming to optimize production, ensure quality, and enhance efficiency. With a plethora of options available in the market, discerning the right machine can be a daunting task. This article delves into five key indicators that can guide you in making an informed decision.
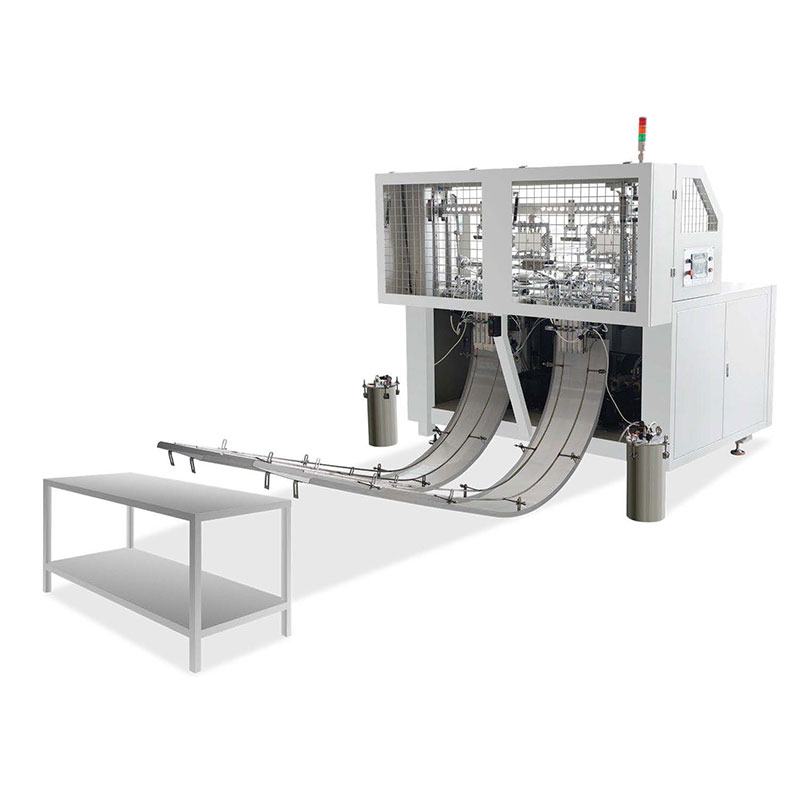
Burger Box Making Machine
Production Capacity: Meeting Demand Head-On
The production capacity of a burger box making machine is a fundamental consideration. It directly impacts your ability to meet market demand, especially during peak seasons or when faced with large orders. Assessing your daily, weekly, or monthly production requirements is the first step. If you operate a bustling fast-food chain with high-volume sales, a machine capable of producing a substantial number of boxes per hour is indispensable. For instance, a busy outlet might need a machine that can churn out 500 to 1000 burger boxes per hour. On the other hand, a small-scale bakery or a startup food business with lower demand can opt for a machine with a more modest production capacity, perhaps 100 to 300 boxes per hour.
When evaluating production capacity, also consider the machine's speed consistency. A machine that can maintain a steady production rate without compromising on quality is ideal. Some machines offer variable speed settings, allowing you to adjust the production rate based on your immediate needs. This flexibility can be a boon, especially when you need to ramp up production during rush hours or slow it down for quality checks.
Material Compatibility: Ensuring a Perfect Fit
The type of material you intend to use for your burger boxes plays a crucial role in machine selection. Burger boxes are commonly made from materials such as cardboard, paperboard, or specialty food-grade papers. It is imperative that the machine you choose is compatible with your chosen material. Different machines are designed to handle specific material thicknesses and types. For example, if you plan to use thick, high-quality cardboard for a premium burger box line, ensure the machine can handle the material without jamming or causing damage.
Material compatibility also extends to the machine's forming and sealing mechanisms. Some materials may require specific types of glue or heat-sealing techniques. A machine equipped with a water-based adhesive system may be suitable for certain paperboard materials, while others may demand a different adhesive application method. Additionally, consider the machine's ability to handle recycled or eco-friendly materials if sustainability is a priority for your business. As consumer demand for environmentally conscious packaging grows, having a machine that can work with sustainable materials can give your business a competitive edge.
Size and Shape Versatility: Adapting to Market Trends
The food industry is ever-evolving, with changing consumer preferences and innovative burger presentations. This calls for a burger box making machine that can adapt to different box sizes and shapes. A versatile machine can produce boxes in various dimensions, from small snack-sized boxes to larger ones for double or triple burger combos. It should also be capable of creating different box shapes, such as square, rectangular, or even uniquely designed boxes to make your product stand out on the shelves.
Look for machines that offer easy adjustment mechanisms for box size and shape. Some advanced models come with digital controls that allow you to input the desired dimensions, and the machine automatically adjusts its settings. This not only saves time but also ensures accuracy in production. The ability to switch between different box sizes and shapes quickly can give you the flexibility to respond to market trends and customer requests promptly. Whether it's a special promotional box or a new product launch, a versatile machine can help you meet the packaging needs without the need for extensive retooling.
Automation Level: Balancing Efficiency and Cost
The level of automation in a burger box making machine can significantly impact your production process and bottom line. Fully automatic machines offer a high degree of efficiency, handling tasks such as paper feeding, box forming, gluing, and stacking with minimal human intervention. They are ideal for large-scale production environments where speed and consistency are paramount. However, they also come with a higher price tag and may require more complex maintenance.
Semi-automatic machines, on the other hand, offer a more cost-effective solution for businesses with lower production volumes or those on a budget. These machines typically require some manual input, such as loading the paper or adjusting certain settings, but still automate key processes like box forming and gluing. They provide a balance between cost and efficiency, allowing you to produce a reasonable number of boxes while keeping labor costs in check. When deciding on the automation level, consider your production requirements, budget, and the availability of skilled labor. A fully automatic machine may be a wise investment if you anticipate significant growth in your business, while a semi-automatic one can be a practical choice for startups or small to medium-sized enterprises.
Quality and Durability: A Long-Term Investment
Investing in a high-quality burger box making machine is essential for ensuring consistent product quality and long-term reliability. A well-built machine is less likely to experience breakdowns, reducing production downtime and maintenance costs. Look for machines constructed from robust materials and with precision-engineered components. The machine's frame should be sturdy enough to withstand continuous operation, and its moving parts should be designed for smooth and efficient performance.
Quality also extends to the finished product. A good machine should produce burger boxes with clean edges, precise folds, and secure seals. This not only enhances the aesthetic appeal of the boxes but also ensures the integrity of the food products they contain. Check the machine's reputation in the market by reading customer reviews and testimonials. A machine that has a track record of delivering high-quality output and reliable performance is more likely to be a worthy investment. Additionally, consider the manufacturer's warranty and after-sales support. A comprehensive warranty can give you peace of mind, knowing that you are protected against any potential defects or malfunctions in the machine.
In conclusion, choosing the right burger box making machine requires a careful evaluation of these five key indicators. By considering production capacity, material compatibility, size and shape versatility, automation level, and quality and durability, you can make a decision that aligns with your business goals, production needs, and budget. Remember, a well-chosen machine is not just a piece of equipment; it's an investment in the success and growth of your food packaging business.